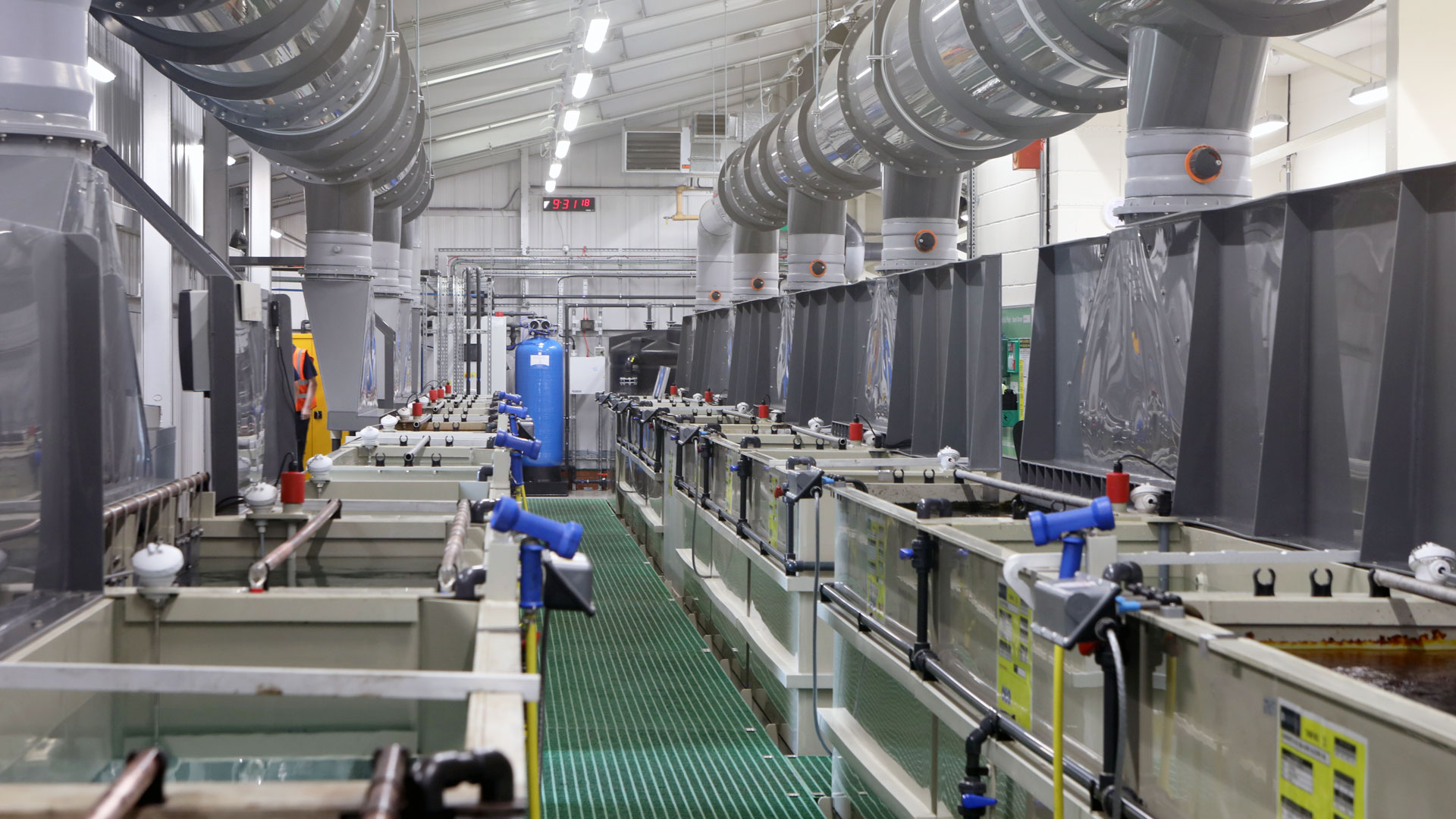
Parts and components manufacture
Marshall’s in-house parts and components manufacturing team produces high-quality, certified aerospace parts and components, backed by state-of-the-art equipment and decades of expertise.
Our Part 21G and NADCAP-accredited facility in Cambridge, UK, can undertake all aspects of high-complexity manufacturing for military and civil customers alike, serving as a single source for finished parts or turnkey sub-assemblies.
One team supporting C-130 availability
Marshall has nearly 60 years of experience providing full lifecycle maintenance, repair, overhaul (MRO) and engineering for the Lockheed Martin C-130 Hercules platform. Fleet operators around the world value our ability to independently produce, repair and refurbish parts and components with OEM-level authority to manufacture.
We produce roughly 2,000 parts per year on average across legacy C-130 models and the current production C-130J Super Hercules. We are proud to have manufactured more parts for more C-130 operators than any other MRO organisation.
For parts that are difficult to obtain or have particularly long lead times, in-house production can significantly de-risk the maintenance process, enhancing fleet availability by making turnaround times more predictable and dependable. Similarly, we are able to respond at short notice to emergent work arising from the discovery of defects during routine maintenance process.
Marshall’s integrated project team (IPT) approach guarantees a seamless experience, as our manufacturing support specialists remain in constant contact with the teams working on the aircraft in our hangars.
Fully integrated manufacturing
Marshall’s expertise extends beyond the C-130: we have developed the skilled workforce, equipment and accreditations to take civil or defence aerospace parts, components or subsystems from drawing to finished product. In fact, since 2021 we have produced more than 6,000 non-C-130 parts.
Our vertically integrated facility houses every stage of the production process, including complex machining, sheet metalwork, assembly, inspection, testing, treatment and paint.
For our customers, working with Marshall from start to finish avoids the complexity, cost and risk associated with subcontracting. We also provide complete transparency throughout the process, from materials and supply chain to manufacture, inspection, treatment and delivery.
Explore our full range of capabilities below:
-
Production
- Production engineering
- CNC programming
- CNC milling and turning
- Manual milling and turning
- FDM additive manufacturing (3D printing)
- Engraving
- Tool making
- Honing and grinding
- Sheet metalwork
- Pipework
- CMM inspection
- Manual inspection
-
Special Processes
- Heat treatment
- Surface treatments
- Chromate conversion coating
- Chromic anodising
- Sulphuric anodising
- CRS passivation
- Painting
- Non-Destructive Testing
- Welding
-
Assembly
- Mechanical assembly
- Electrical assembly
- Systems assembly
Manufacturing approvals
Our manufacturing support facility is NADCAP-accredited and holds approvals from Boeing and Lockheed Martin for welding, testing, chemical processing and heat treatment of materials.
Accreditation | Certifying Body | Customer |
---|---|---|
AS9100 QMS | AFNOR | Boeing |
EU 1702/2003 Part 21G | UK CAA | |
Heat Treatment | NADCAP | Boeing, Lockheed Martin |
Chemical Processing | NADCAP | Boeing, Lockheed Martin |
Welding | NADCAP | Boeing, Lockheed Martin |
NDT | NADCAP | Boeing, Lockheed Martin |