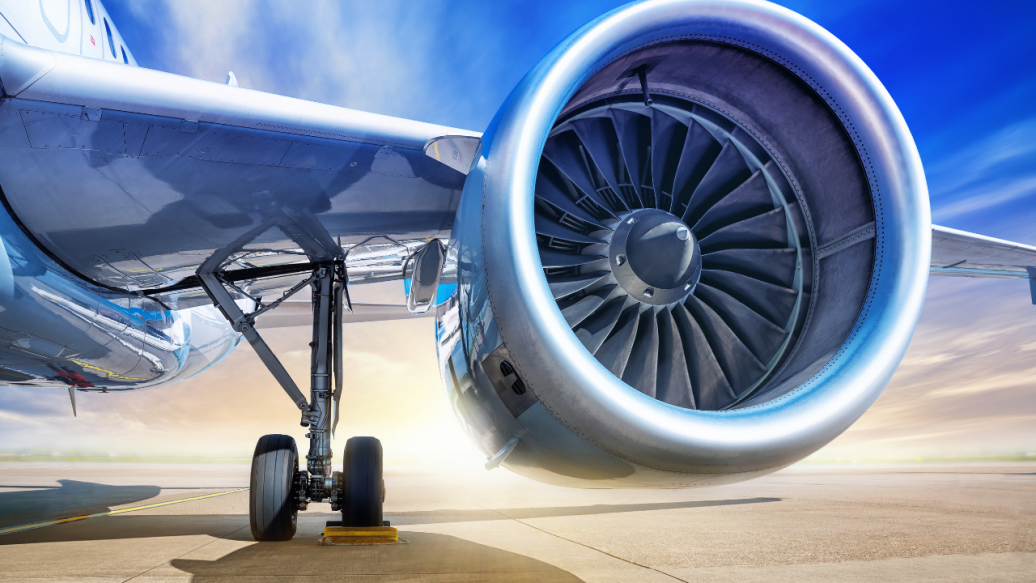
Marshall Centre welcomed a group of MBA interns from Westminster University to join us for three months to bring a fresh, outside perspective to some of the projects we are currently working on. One of those projects involves looking at the future of aviation, how technology, sustainability and efficiency will drive innovation, and how we adapt our training packages to meet our valuable customers’ needs in the next 30 years.
We spoke to Adam Poole from Contrado. Adam is a hardware engineer who designs electronic systems predominantly for the aerospace industry, who discussed the ways that disruptive technology will effect the future skills that aircraft maintenance teams will need in future. This insider knowledge from someone who started as an engineering apprentice and is now designing the technology for the future of aviation was invaluable. In this article, we will highlight some of the key points that Adam made.
Aviation lifecycles
If you look at aerospace and what aeroplanes look like today versus what they looked like when the Wright brothers first took to the sky, you will find many features have not changed significantly. Similarly, if Karl Benz were alive today and you asked him to identify parts in a modern Mercedes, he would probably recognise 90% of them. Although we have far more sophisticated technology in our vehicles now, the basic mechanics have not changed much in the past 140 years. Aviation works in lifecycles, which is much slower than our consumer products such as cars and this is mainly due to the cost of designing, manufacturing, and maintaining aircraft. Although engineers are brilliant and they can come up with innovative ideas that will solve all the worlds problems tomorrow, they are limited by budgetary constraints. So, the lifecycle of aircraft is much longer, and the skills needed to maintain them safely has not changed much in the past 60 years. However, the industry must become more environmentally friendly so we will see rapid change in the next few decades.
Where does new technology in aviation originate?
The western civil aviation industry is currently dominated by two big players: Airbus and Boeing. Other companies who have dominated the small jet market include Embraer and Bombardier, but they mainly sell regional jets and not many of the large intercontinental jets. Regardless of the size of the aircraft, all these companies source their parts from the same group of suppliers like GE or Rolls Royce and these are the companies who design the revolutionary technology for aircraft of the future. Boeing and Airbus are systems integrators, which means that they do not tend to design hardware, instead, they write a requirements specification of what they want their next aircraft to be able to do.
Priorities for commercial airlines
As new aircraft are designed there is a major factor to consider and that is the environmental impact (CO2 output) of operating those aircraft. Green technology and sustainability are hot topics as we head towards becoming carbon neutral by 2050. Passenger and freight aircraft were responsible for emitting 1.04 billion tonnes of carbon dioxide in 2018, so designing aircraft with greater fuel economy and less CO2 emissions is high on the agenda. This means that technology must change to reduce the weight of the aircraft and increase its aerodynamic efficiency.
The structure of the aircraft
If you designed an aircraft in the 1950s, you would have built the fuselage from aluminium as it is strong, plentiful and lightweight. There is a cost involved in processing it, but it was the best material to use for those early models. All the Boeing aeroplanes up until the 787 were all made from aluminium. Airbus aircraft, on the other hand, have been increasingly made from composites (two or more materials with different chemical and/or physical properties combined) and this is to do with weight saving. If an aircraft is lighter, it requires less energy. Therefore, this is the first thing that is going to change across the industry; new aircraft will be lighter in weight.
What happens to older aluminium aircraft?
The Boeing 747 was designed in the 1950s and it is still flying today; there are second-hand 747s that have been bought and operated by poorer 3rd world operators that are 60+ years old and still in use. They were built to withstand vast extremes of temperature and stress, but like all metals, cracks and weaknesses will start to appear in the aluminium structure over time due to fatigue, stress and corrosion. So, before these aluminium aircraft take off, a maintenance engineer carries out pre-flight safety checks, where they inspect, monitor, and log any damage that they see. Like all mechanical components, aircraft parts fail and corrode over time, so it is important from a safety perspective that any significant damage is identified. Roughly 60% of the cost of the aircraft is in the wings, so significant wing damage in older aircraft is normally the catalyst to retire the aircraft rather than fix it. Over the next few decades, aluminium aircraft will start to disappear and be replaced by composite aircraft.
Find out what happens to aircraft when they retire.
Why composite aircraft are different
Like large buildings, composite aircraft have steel and titanium components in the structure to give it tensile strength. However, unlike aluminium aircraft, you cannot inspect a composite aircraft externally for damage and cracks, meaning maintenance teams cannot see where the cracks are forming on the internal steel and titanium components without the use of specialist measuring equipment. If passengers thought that there was a chance that part of the aircraft could fall off mid-flight, they would be unlikely to buy a ticket, which is not good for business. Thankfully, it is unlikely to happen now as all the composite aircraft in the sky today are relatively young, but the day is coming that someone, somewhere will want to push these aircraft to operate for 60 years. It is easy to say retire them all after x number of years, but that will mean that the cost of flying will increase for passengers. In the past few decades, airlines have found a way to make air travel extremely affordable and this has allowed for greater global mobility, so we do not want to go back to a time where flying was an expensive and exclusive way to travel. This means that in the next few decades, MRO’s will need to consider training for their teams on newly developed systems and technologies that allows them to continue maintaining older composite aircraft safely, and new certificates will likely be issued by the FAA to address issues related to the longevity of composite aircraft.
What does the future of air travel look like?
If you have flown in a commercial aeroplane, it more than likely had Gas Turbine engines. You may have flown in a piston engined aircraft if you have visited a small island or remote location, but most commercial aircraft that fly long-distance have Gas Turbine engines that burn fuel to provide thrust. Although these engines have become more fuel-efficient over the years, they still produce high levels of CO2 emissions. The way the industry is looking to solve this problem and make short-haul air travel greener is by designing autonomous propeller-powered aircraft with net-zero emissions. There are many new, innovative aviation companies emerging such as Lilium, Vertical Aerospace and Faradair (just to name a few). These companies are receiving attention and investment as they are disrupting the aviation industry and redefining the way we travel.
What are the advantages of travelling in an air taxi?
Autonomous air taxies will completely change the way we travel in future. Considering the current flying model, if you are in Cambridge and you want to travel to Munich, the time you spend in the air is roughly 45 minutes. However, that trip takes roughly 5 hours door to door because of the time you spend in the airport. If someone said to you that you could call an air taxi to a dedicated air taxi rank, and the vehicle could take off and land vertically, your door-to-door journey will be reduced to an hour and a half, not only saving time but also money. However, these autonomous vehicles will still require highly skilled maintenance teams and new safety regulations to ensure air travel remains the safest form of transport.
Will we still travel on large aircraft?
Although there are many new promising start-ups in aviation, it is unlikely that Boeing and Airbus will easily let go of their oligopoly as they are both backed by governments and there is too much money tied up in them. Unfortunately, like most start-ups, many of these new entrants will fail. However, there are a few (mentioned previously) who show significant promise and stand a good chance of cornering the market with their ultra-lightweight, autonomous, propeller aircraft that transport small numbers of people across short distances. The same propeller technology is not yet scalable to larger aircraft that are produced by Boeing and Airbus and that may only happen in the very distant future. However, there will still be a need to carry hundreds of people to destinations on one aircraft, so the technology shift for those larger aircraft manufacturers will be towards biofuel, hydrogen, or hybrid aircraft that use less fuel. We may still need jet fuel for take-off and landing as those processes require more energy than cruising in the air, which can be powered using electric energy.
How will these changes impact the skills our future aircraft maintenance teams need?
Most engineers today are hardware engineers who understand power electronics as most aircraft today have jet engines. Also, the actuation of the ailerons and other systems on the aircraft is mainly controlled by hydraulics, so our current maintenance training packages focus on those kinds of skills. However, that will change in future as the aircraft of tomorrow will likely ditch all hydraulic systems, so the industry will need more people with wiring capability and understanding of electronic systems. This is due to the introduction of wide band gap transistor technologies, which allow for greater power efficiency in smaller, lighter weight components like silicon carbide and gallium nitride. This changes what we can do with power electronics because engineers can take weight out and move energies around in a way that we could not do 15 years ago.
Recycling wasted energy
Commercial electronics are designed to work between 0 to 70 degrees centigrade, but aerospace components have a temperature range of -55 to 124 degrees centigrade. When you are flying high up in the atmosphere is gets very cold and this means that ice can form on the wing and if that happens, the wing no longer functions as a wing, which is not helpful when trying to keep an aircraft in the sky. To stop ice from forming, engineers created bleed air systems, which takes some of the warm, compressed air from the jet engines to heat aircraft and prevent ice from forming on the wings, or pneumatic systems that require a vacuum source derived from the bleed air system. Recent advances in technology mean that engineers no longer need to use bleed air systems and can replace them with electrothermal de-icing, which has fuel-saving benefits. However, there is only one model of aircraft in operation today using that technology and that is the Boeing 787, so the need for skilled workers who understand how to maintain that aspect of the aircraft is still low, but in future, all aircraft will use that technology so there will be a surge in the need to close that skill gap.
The main takeaways from the MBA intern’s presentation and the intel gathered from Adam Poole, is that MRO’s must start thinking about the types of skills they need their people to have to be able to maintain the next generation of aircraft that they will start to see in their hangars in the next few years.
Click here to contact our team of aviation experts to discuss your training needs.